Understanding What is Porosity in Welding: Reasons and Solutions
Understanding What is Porosity in Welding: Reasons and Solutions
Blog Article
Porosity in Welding: Identifying Common Issues and Implementing Best Practices for Prevention
Porosity in welding is a prevalent concern that usually goes unnoticed until it causes significant troubles with the integrity of welds. In this discussion, we will explore the key factors contributing to porosity formation, examine its destructive effects on weld performance, and discuss the finest methods that can be embraced to lessen porosity occurrence in welding procedures.
Usual Root Causes Of Porosity
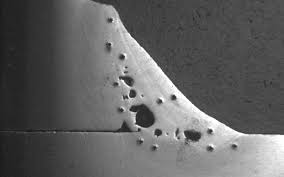
Another regular perpetrator behind porosity is the existence of impurities externally of the base steel, such as oil, oil, or corrosion. When these contaminants are not properly gotten rid of prior to welding, they can evaporate and end up being caught in the weld, triggering problems. Additionally, using dirty or damp filler materials can present contaminations right into the weld, adding to porosity issues. To reduce these typical root causes of porosity, detailed cleaning of base metals, proper protecting gas option, and adherence to optimal welding specifications are crucial methods in attaining premium, porosity-free welds.
Impact of Porosity on Weld High Quality

The presence of porosity in welding can significantly endanger the structural honesty and mechanical homes of bonded joints. Porosity creates voids within the weld steel, deteriorating its total strength and load-bearing capacity.
One of the key effects of porosity is a decrease in the weld's ductility and toughness. Welds with high porosity levels have a tendency to show reduced influence stamina and reduced ability to warp plastically before fracturing. This can be particularly concerning in applications where the welded elements are subjected to vibrant or cyclic loading problems. Furthermore, porosity can hamper Home Page the weld's ability to effectively transfer forces, causing early weld failure and potential safety and security threats in essential frameworks.
Ideal Practices for Porosity Prevention
To improve the architectural integrity and quality of welded joints, what certain actions can be implemented to lessen the event of porosity throughout the welding procedure? Making use of the correct welding strategy for the particular material being bonded, such as adjusting the welding angle and weapon setting, can additionally avoid porosity. Routine additional resources assessment of welds and prompt removal of any kind of concerns recognized throughout the welding procedure are crucial techniques to protect against porosity and generate high-grade welds.
Importance of Proper Welding Techniques
Executing correct welding methods is paramount in guaranteeing the structural stability and high quality of welded joints, developing upon the foundation of efficient porosity avoidance procedures. Excessive warmth can lead to enhanced porosity due to the entrapment of gases in the weld swimming pool. special info Furthermore, using the ideal welding specifications, such as voltage, present, and take a trip speed, is vital for achieving sound welds with minimal porosity.
In addition, the option of welding procedure, whether it be MIG, TIG, or stick welding, should straighten with the details demands of the project to make sure optimum results. Appropriate cleansing and preparation of the base steel, along with picking the right filler material, are additionally important elements of competent welding strategies. By sticking to these best methods, welders can decrease the risk of porosity formation and create high-quality, structurally sound welds.
Evaluating and Quality Assurance Measures
Quality assurance steps play a crucial role in confirming the honesty and reliability of welded joints. Checking treatments are important to spot and avoid porosity in welding, making certain the stamina and resilience of the end product. Non-destructive screening methods such as ultrasonic testing, radiographic testing, and visual assessment are generally used to identify potential problems like porosity. These strategies permit the assessment of weld top quality without compromising the stability of the joint. What is Porosity.
Post-weld examinations, on the other hand, evaluate the final weld for any kind of problems, consisting of porosity, and confirm that it fulfills defined standards. Carrying out a comprehensive quality control strategy that includes comprehensive screening treatments and evaluations is critical to lowering porosity problems and making certain the general high quality of welded joints.
Final Thought
To conclude, porosity in welding can be a typical problem that affects the high quality of welds. By identifying the typical reasons of porosity and implementing finest methods for avoidance, such as correct welding techniques and testing measures, welders can ensure excellent quality and trusted welds. It is important to focus on prevention methods to reduce the incident of porosity and preserve the stability of welded structures.
Report this page